Exploring the Global Manufacturing of Toyota Trucks
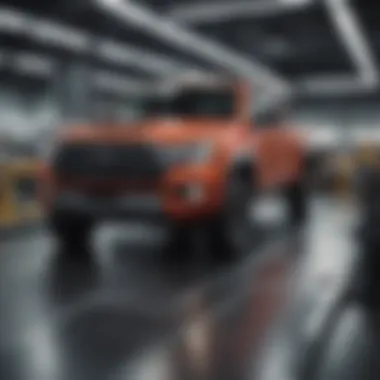
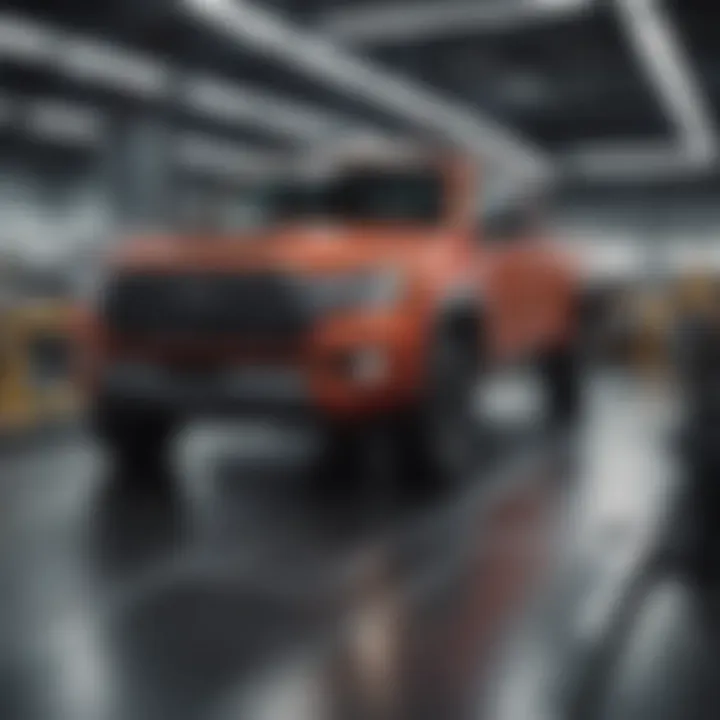
Intro
Toyota has established itself as a formidable player in the global automotive market, particularly known for its trucks. Understanding where these trucks are produced can provide important context about their manufacturing quality, and it reveals something about Toyota's strategic approach. Together, these elements provide insight into local economies, the supply chain, and ultimately, consumer impacts.
In this article, we will explore the various global manufacturing plants dedicated to the production of Toyota trucks. The discussion will reveal the interconnected nature of production strategy, technological impact, and even economic effects.
Car Reviews
Overview of the Vehicle
Toyota trucks encompass a range of models designed to cater to diverse consumer needs and lifestyle requirements. Models like the Tacoma and Tundra vary in size and specifications but share a reputation for durability and reliability. An organic understanding of these vehicles starts with where and how they are made.
Performance Analysis
Manufacturing quality greatly influences performance capabilities. The Tacoma, known for its off-road prowess, benefits significantly from production standards upheld in several Toyota facilities. Each plant incorporates advanced manufacturing techniques tailored to ensure these trucks endure their intended use.
Design and Interior Features
While utility is a hallmark of Toyota trucks, design choices also play an important role. Taking inspiration from consumer feedback, interior layouts have evolved to offer both comfort and functionality. Different plants may embody cultural influences that shape design, threading local norms into global production.
Safety Ratings and Specifications
Safety is a constant priority in the automotive industry. Toyota adheres to stringent international safety regulations across its manufacturing sites. Each truck undergoes standardized testing that can slightly differ by location, but the results reflect a dedicated commitment to consumer safety.
Value for Money
Assessing the value of Toyota trucks largely hinges not only on the sticker price but also on the perceived reliability and resale value. Local manufacturing may impact costs and availability, thereby enhancing the overall financial proposition for potential buyers.
Automotive Industry Trends
Emerging Technologies
In the quest for innovation, Toyota continues to spearhead developments in vehicle technology. Factories are slowly introducing robotic assistance and smart analytics, optimizing the assembly line processes semi-automatically.
Changes in Consumer Preferences
Although popularity sways towards fuel-efficient vehicles, the versatility of Toyota trucks suits a persistent demand. As buyers prioritize functionality, observations regarding modularity and customization emerge prominently.
Sustainability and Eco-Friendly Practices
Environmental considerations significantly influence current production strategies. Efforts are underway within all plants to reduce carbon emissions during the manufacturing phase. This goes hand-in-hand with the engines used in both hybrid models and traditional setups.
Future of Electric Vehicles
Looking ahead, the transition towards electric vehicles gains traction in the Toyota lineup. Production technology will likely pivot in line with evolving regulatory frameworks and consumer preferences, heralding promising advancements.
Industry Challenges and Solutions
Every automotive manufacturer faces challenges within the ecosystem. Supply chain disruptions during global crises have exposed vulnerabilities. In response to these, Toyota exhibits adaptability, reconsidering logistics and production strategies to remain resilient.
“Understanding where Toyota trucks are made invites deeper insights into the company’s reach, strategy, and adaptability in fluctuating markets.”
Buying Guides
How to Choose the Right Vehicle
Choosing the right truck requires careful consideration—not just of model specifics but also where they originate. Analyzing production locations can also guide buyers in assessing regional-specific features.
Financing and Insurance Tips
Prior to purchase, understanding insurance implications related to truck models can yield financial insight, especially if certain regions have established differences. Addressing financing transactions requires attention to interest rates tied with extended warranties offered by differing plants.
Common Mistakes to Avoid
Common oversights when buying trucks can often involve underestimating diesel versus gasoline consumption. Furthermore, overlooking warranty conditions linked to region-specific availabilities can impact long-term satisfaction.
Maintenance and Ownership Considerations
Regular maintenance routines deserve awareness if trucks are manufactured in varied locations. Educational resources may exist for owners reflecting on model durability challenges directly influenced by manufacturing strategies.
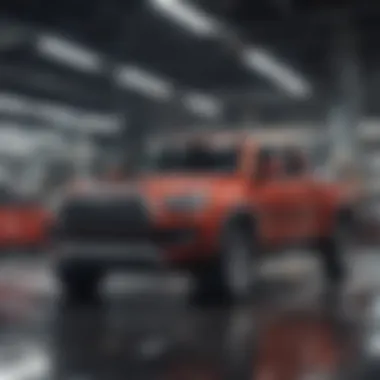
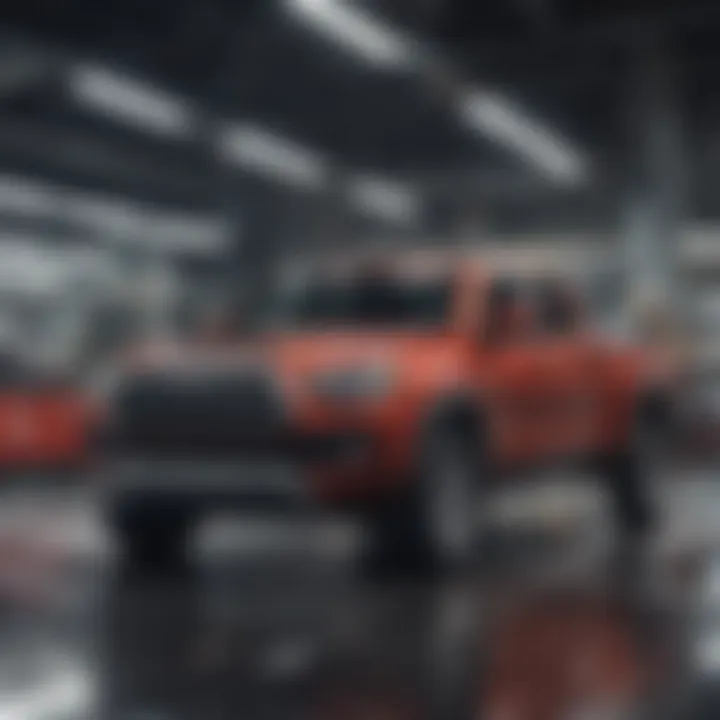
Resources for Further Research
For readers eager to investigate deeper, consider consulting education platforms like Wikipedia, Britannica, or communities on Reddit. Each source can extend the knowledge around Toyota trucks and their complex manufacturing architecture.
Toyota's Global Manufacturing Footprint
The manufacturing approach of Toyota is a prime aspect that encapsulates its operational success. This global footprint revitalizes the brand, ensuring increased accessibility for consumers while maintaining quality standards. Understanding where Toyota trucks are made reveals not only the geographical variance but also the strategic insight of the company into local markets.
Toyota’s presence across multiple continents highlights its adaptability. By establishing robust plants in strategic locations, Toyota minimizes shipping costs and time, making it easier to respond to regional consumer preferences. Such operational efficiency often results in better pricing for the end consumer and significantly contributes to the brand's reputation for reliability.
The flexibility in Toyota’s manufacturing process allows for a diverse production mix. Whether it’s fulfilling demand for smaller vehicles or rugged trucks, the ability to switch production lines quickly boosts responsiveness to market changes. This reactivity is useful in hospitality markets, where trends can shift.
Overview of Production Facilities
Toyota operates numerous production facilities around the world, each tailored to meet specific local needs and to follow corporate guidelines for quality and efficiency. These plants vary widely in size and technological sophistication but share a common commitment to uphold Toyota's well-known standards. Production facilities have become not just locales of productivity but also innovation centers identifying new ways to enhance processes.
Facilities in the United States exemplify a classic investment in local manufacturing. Two major planta, located in Texas and California, are primarily focused on truck production. Additionally, Toyota operates several essential facilities in other parts of Asia and Europe, allowing shared technology and strategies that ensure unified quality levels across all manufactured trucks.
Toyota's distribution network relies heavily on these integrated facilities. By connecting the sales process directly with manufacturing, Toyota reduces bottlenecks. Furthermore, it allows for rapid on-demand production that keeps inventory low while meeting market needs more effectively.
Historical Development of Manufacturing Sites
The historical backdrop of Toyota's manufacturing strategy uncovers a gradual yet decisive expansion. Starting in Japan, Toyota predominantly operated within its national borders, focusing first on the domestic market. As the company growsd, it established plants internationally, with the first American assembly operation opening in 1984 in California. This progressive shift influenced not only the company’s operations but also the entire automotive market in the U.S.
Developments in Japan’s automotive culture also played a crucial role, as low production costs and advanced technology set a model for efficiency. As Toyota began to penetrate different markets, it adapted to local conditions, demonstrating a keen understanding of reactive production methods.
As a result, each new plant inaugurated influences the company's direction. Lessons learned from one site are often replicated at others, establishing a continuous improvement model. This strategy exemplifies not just a business expansion, but a fundamental shift in approach across borders – promoting a culture of localized production within a global framework.
The careful balance between global outreach and local adaptation is reflective of Toyota’s ethos: efficiency and quality first.
In cohesive terms, the development of these facilities speaks volumes about Toyota’s ambition and connectivity in the global economy. The rich blend of tradition with modern business methods continues to redefine what it means to produce over multiple geographies.
Key Locations for Toyota Truck Production
The relevance of Toyota's truck production facilities cannot be overstated. These locations are central to the company's strategy for manufacturing. Their geographical diversity offers specific advantages, shaping both the production efficiency and quality of the trucks produced. Each factory is strategically placed to cater to local markets, thereby enhancing logistic capabilities and adapting to consumer demands efficiently.
United States Manufacturing Plants
San Antonio, Texas Facility
The San Antonio facility plays a crucial role in Toyota's production strategy. Operational since 2006, it focuses primarily on the assembly of the Tundra and Tacoma trucks. One key characteristic of the San Antonio plant is its integration of advanced automation technologies which boosts efficiency and accuracy in manufacturing.
This facility is particularly beneficial as it significantly meets the demand for these models within the North American market. The plant's unique feature is its large manufacturing capacity, capable of producing up to 200,000 trucks annually. This high-output arrangement lends Toyota an advantage in a competitive market. It also foster local economic growth creating jobs in the area.
However, challenges do exist, particularly in the fluctuating demand for trucks, which can impact production levels and staffing.
California Plant
Toyota's California plant, located in Fremont, has a different focus. While it does not produce trucks in mass quantities like its Texas counterpart, it contributes to the local economy and embodies Toyota's commitment to hybrid technologies. This plant is key for producing models that incorporate advanced environmental standards, thus appealing to environmentally-conscious consumers.
One distinct feature of the California plant is its emphasis on producing zero-emission vehicles. This aligns with Toyota's broader sustainability goals, making it a beneficial location for consumers interested in reducing their carbon footprint.
On the downside, the operation of this facility comes with higher labor costs compared to other sites, which affecting profit margins and pricing strategies.
International Manufacturing Plants
Japan Production Facilities
Toyota's roots are in Japan, and its production facilities here remain integral to the brand's identity. The plants in Japan are known for their rigorous quality control measures, ensuring trucks are made with the highest standards. One key characteristic of these facilities is their implementation of the Toyota Production System, which focuses on eliminating waste and enhancing operational efficiency.
These facilities contribute significantly to the overall production of various Toyota models, including trucks. Their unique advantage lies in the access to engineering expertise and innovation which these facilities foster and promote within the global landscape of automotive production. Popularly regarded as hubs for superior craftsmanship, Japanese facilities are the backbone of distinguishing the brand's quality.
However, production costs in Japan are higher due to labor expenses and stricter regulations resulting in increased pressure to balance quality and profitability.
Thailand Manufacturing Site
The Thailand manufacturing site is crucial for Toyota's international presence. Located in Samut Prakan, it's specifically significant for producing small and mid-size trucks. Its key characteristic is its lower production costs, which significantly optimize Toyota's supply chain and pricing structure.
This location serves an expanding market in Southeast Asia; hence the site is pivotal for Toyota's strategy to provide cost-effective vehicles that fit consumer preferences in that region. The unique feature is also its close proximity to key automotive suppliers, allowing for efficient sourcing of materials.

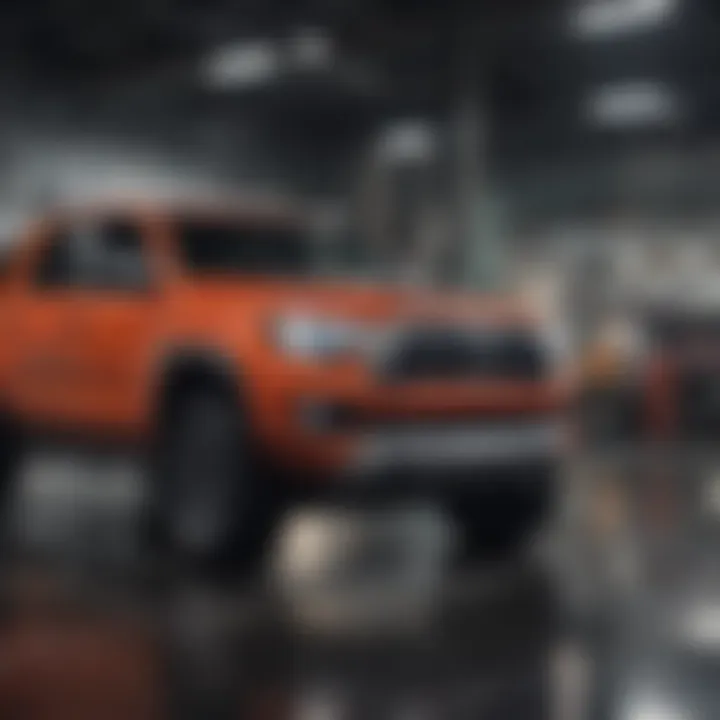
Yet, like any operation, the plant also faces challenges, especially fluctuating economic conditions in the surrounding areas which can affect demand.
By maintaining both U.S. and international facilities, Toyota demonstrates a commitment to agile manufacturing that adapts to regional market needs while sustaining quality excellence across its truck production.
The Impact of Local Economies
Automotive production is closely intertwined with the economic landscapes of the regions in which companies operate. This impact becomes particularly evident when we focus on Toyota trucks and the ecosystems surrounding their manufacturing plants. Understanding how local economies are shaped by these plants is essential not only for grasping the overall significance of Toyota's operations but also for recognizing the multifaceted benefits they bring to communities.
Economic Contributions of Toyota Plants
Toyota factories play a crucial role in local economies. They do not just manufacture vehicles; they contribute significantly to overall economic activity. This contribution can be broken down into several key areas:
- Direct Economic Impact: Manufacturing facilities create jobs not only in the plant itself but also in the supply chain. These plants frequently partner directly with local suppliers for parts and materials, further stimulating the economy.
- Tax Revenues: Operations of these facilities generate substantial tax revenues for local, state, and federal governments. This revenue can then be reinvested into public services and infrastructure improvements.
- Investment in Infrastructure: Toyota often collaborates with government agencies to enhance local infrastructure, which may include roads and utilities. Such improvements benefit both the company and the community, facilitating better access to facilities and services for residents.
Toyota's plants in the United States, particularly in Texas and California, explicitly demonstrate these economic contributions, enhancing the surrounding community's financial health.
Job Creation and Community Engagement
The role of Toyota in job creation cannot be underestimated. Each manufacturing facility often employs thousands of workers, providing stable job opportunities in various sectors.
Engagement with the local community is essential to Toyota’s operations. The company frequently embarks on initiatives aimed at fostering community relations.
- Local Hiring Practices: Toyota makes concerted efforts to hire locally, enhancing economic stability in the surrounding area. Hiring local workers not only provides employment but also helps build a loyal and dedicated workforce.
- Support for Community Programs: Toyota is known for its commitment to corporate social responsibility. The company invests in local educational programs, scholarships, and various community development initiatives.
“Companies like Toyota, with strong ties to their local communities, can transform the region’s economic landscape as perfectly as they shape their product innovations.”
In summary, the impact of local economies is deeply felt wherever Toyota plants operate. These facilities not only produce trucks but also fuel economic health, contributing to job opportunities and enhancing community engagement. Through their various initiatives, Toyota demonstrates an ongoing commitment to supporting and enhancing the regions in which they operate.
Supply Chain Considerations
In understanding where Toyota trucks are made, it is essential to consider the supply chain. The supply chain serves as the backbone of manufacturing and has profound implications on efficiency, quality, and even the sustainability of the vehicles produced. Having well-structured logistics and supplier linkage impacts not only the costs of production but also affects the timelines of delivery and the overall performance of the trucks.
Logistics in Truck Production
Effective logistics are crucial for producing Toyota trucks. These logistics are defined by various factors, including transportation methodologies, warehousing practices, and distribution networks. With specific plants situated across the globe, formation of a seamless logistical framework allows for complex interactions among different production sites.
Some critical attributes of logistics in truck production include:
- Timely delivery: Components must arrive just in time for assembly. This minimizes storage costs and reduces the risk of part obsolescence.
- Coordination between facilities: Movement of parts from global and local suppliers needs careful coordination to maximize efficiency.
- Inventory management: Toyota employs a just-in-time system that allows them to adjust inventory based on real-time needs, avoiding excess stock and streamlining operations.
Overall, these logistics shapes the quality of manufacturing. If any element fails, it can ripple through the production process.
Material Sourcing and Local Partnerships
Material sourcing plays an essential role in manufacturing, particularly for trucks. Toyota actively seeks to construct meaningful partnerships with local suppliers. These partnerships help the company secure the best materials while boosting local economies. The benefits of local sourcing include:
- Cost reduction: Obtaining raw materials locally can cut down on shipping expenses and office overheads.
- Quality assurance: Toyota maintains strong standards for parts. By sourcing close to the plants, it is easier to inspect quality and compliance, reducing rework and production errors. The criteria set for suppliers often focuses on reliability and permission from Toyota.
- Community collaboration: Working with local businesses fosters growth and resilience within the community where Toyota operates. Such integration enhances Toyota's brand and market acceptance.
Quality Control Measures
Quality control measures are vital in ensuring that Toyota trucks meet the high standards of reliability, performance, and safety that customers expect. For an automotive manufacturer like Toyota, quality is not just a goal; it is essential for maintaining brand reputation and customer satisfaction. The company’s approach combines rigorous testing, employee involvement, and advanced technology. Here, we explore the main elements and benefits of these measures.
Standards in Manufacturing
Toyota employs stringent manufacturing standards influenced by the Toyota Production System (TPS). This system emphasizes the principles of just-in-time production and continuous improvement. Quality standards are backed by clear documentation outlining procedures for every phase of production, from design to final assembly. Additionally, adherence to international safety and quality certifications such as ISO 9001 reinforces this commitment.
Key aspects of these standards include:
- Quality Assurance: Regular audits and assessments.
- Supplier Standards: Ensuring that parts and materials meet rigorous specifications.
- Employee Training: Continuous education on quality practices.
The integration of these elements ensure that any product showing faults can be traced back through the supply chain for rectification, reinforcing overall quality in the manufacturing process.
Continuous Improvement Processes
Continual improvement processes, often referred to as Kaizen in Japanese culture, are foundational in Toyota's quality approach. These processes involve incremental improvements in various areas, rather than drastic changes. Toyota facilitates a work environment that encourages all employees to propose enhancements, creating a culture dedication towards production excellence.
Improvement is measured through several indicators such as:
- Defect Rates: Tracking error trends to minimize failures over time.
- Production Efficiency: Optimizing workflow to reduce waste and improve output.
- Customer Feedback: Utilizing consumer feedback for real-time evaluations and adaptation of production practices.
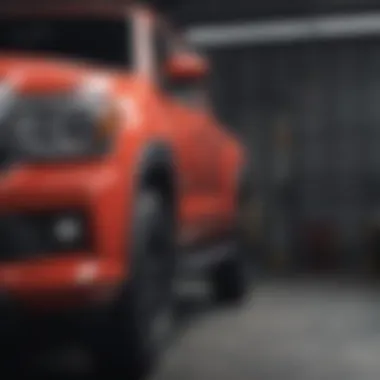
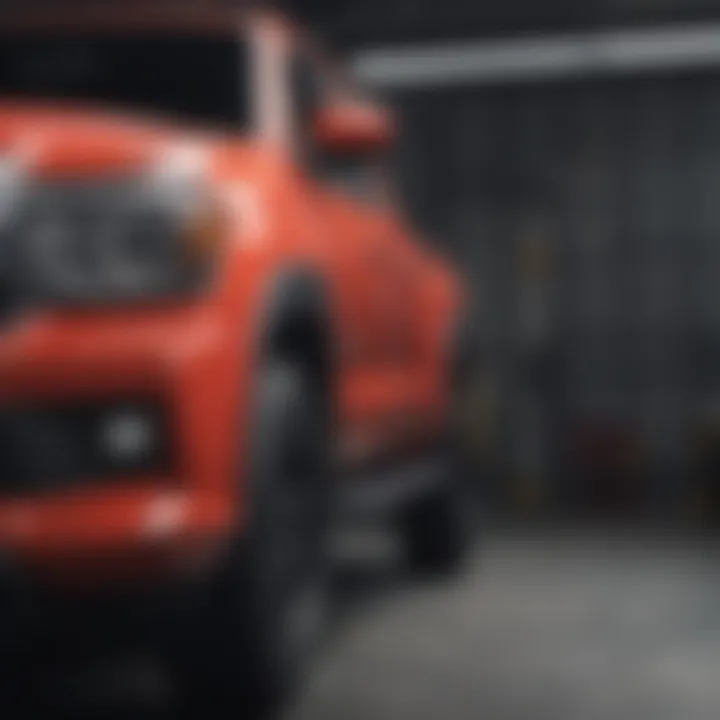
The focus on these aspects not only enhances product quality but also establishes a proactive response to consumer issues, leading to overall better trust in the product's longevity and performance.
The prioritization of quality reflects Toyota's commitment to building trust with consumers in an ever-evolving automotive market.
Through these methodologies, Toyota demonstrates that quality control is not a standalone function but an ongoing commitment ingrained in every facet of their operations.
Future of Toyota Truck Manufacturing
The future of Toyota truck manufacturing holds significant implications for both the company itself and the broader automotive industry. With evolving market demands and intense competition, understanding how Toyota adapts to future challenges is crucial. The incorporation of emerging technologies and sustainability initiatives not only enhances production efficiency but also aligns with consumer expectations for environmentally responsible practices. Focusing on these elements can strengthen Toyota's market position as consumer preferences shift towards innovation and sustainability.
Emerging Technologies in Production
Toyota's integration of emerging technologies into its manufacturing processes illustrates the company's commitment to innovation. Modern manufacturing relies heavily on automation. Robotics and artificial intelligence are essential in optimizing production lines. These tools can predict maintenance needs, minimizing downtime and ensuring that production runs smoothly.
In recent years, 3D printing has gained traction. This technology allows for rapid prototyping and production of parts. It means that parts can be customized more easily and efficiently. Ultimately, less waste occurs in production processes.
Another notable development is the utilization of IoT (Internet of Things). Sensors placed on machinery collect real-time data regarding machine performance. This report helps in identifying inefficiencies in the production process. By analyzing this data, manufacturers can make necessary adjustments quickly. Thus enhancing both productivity and product quality.
Sustainability Initiatives
Sustainability is more than a trend; it is a necessity. Toyota recognizes this and integrates green practices into its manufacturing strategy. Reducing carbon emissions during production is paramount. The company aims to achieve a significant reduction in CO2 emissions from its plants by employing renewable energy sources.
Additionally, Toyota has embraced the idea of a circular economy. This involves not just lessening waste, but reusing and recycling materials. By re-engineering manufacturing processes, Toyota can reclaim materials, leading to less reliance on virgin resources.
Furthermore, initiatives like the Toyota Environmental Challenge 2050 set ambitious goals to promote sustainable practices. The goals focus on enhancing environmental performance, supporting biodiversity, and engaging local communities. Employing these strategies not only meets regulatory requirements but also resonates with today's conscientious consumers.
"Looking ahead, we are committed to pioneering the path towards sustainable manufacturing that reflects our dedication to innovation and environmental responsibility."
With competition tightening, it becomes critical for companies like Toyota to lead within the technology and sustainability landscapes. The upcoming years will involve heightened scrutiny on how firms adapt to these significant shifts — ensuring they align with both market expectations and environmental imperatives.
Consumer Implications
The implications for consumers regarding where Toyota trucks are made extend beyond simple curiosity. Understanding the origin of these vehicles provides valuable insights into several important aspects such as quality, economy, and environmental concerns. Knowing the production locations enables potential buyers to better assess the overall vehicle value as well. Additionally, awareness of manufacturing practices can influence brand loyalty and consumer confidence.
A well-informed consumer can better navigate the automotive market. This knowledge can assist in making decisions based on personal values, as well as support local economies by choosing American-made vehicles when possible. Thus, examining these implications is critical for buyers and enthusiasts alike.
Identifying American-Made Toyota Trucks
Recognition of American-made Toyota trucks hinges on increasingly strict manufacturing labels and guidelines established by the U.S. government. The National Highway Traffic Safety Administration (NHTSA) requires labels on all vehicles specifying where they were manufactured. For many buyers, noting this information is vital. American-made Toyota trucks include notable examples such as the Tacomo and Tundra, both produced at the San Antonio, Texas production facility.
Key aspects to identify:
- VIN Decoding: Each vehicle has a unique Vehicle Identification Number (VIN), which provides crucial information about its production. Japan-manufactured vehicles begin with distinct letter codes compared to those assembled in the United States.
- Manufacturer’s Label: The federal sticker located on the driver’s side door frame includes the country of assembly, giving clear identification.
With such information, buyers can make more informed decisions aligning with their preferences for U.S. manufacturing.
Impact on Vehicle Value
The origin of manufacturing has a significant impact on the value of Toyota trucks. A common perception exists that American-made vehicles maintain better resale value, attributed to local consumer confidence and demand. For example, models produced within the U.S. of the Tundra line often experience higher resale prices than their counterparts built overseas.
Various elements contribute to this value difference:
- Quality Assurance: Vehicles built closer to the consumers may abide by stricter quality controls, positively affecting durability and performance.
- Local Market Preference: American consumers tend to favor vehicles that support local jobs, boosting resale potential.
Essentially, knowing whether a Toyota truck is manufactured in the U.S. or abroad not only influences purchase decisions but also impacts the long-term economic value of the vehicle.
Understanding where Toyota trucks are made influences consumer decisions and ultimately affects vehicle value in the marketplace.
Ending
The exploration of where Toyota trucks are manufactured is essential for a well-rounded understanding of the automotive industry. As noted in earlier sections, Toyota's global manufacturing strategy intricately connects the company to various regions, shaping not only production methods but also local economies. By delving into the manufacturing facilities, the implications for consumers become clearer. This includes an appreciation of regional qualities, motivational aspects behind local partnerships, and highlighting distinct features of each plant.
Without understanding these aspects, consumers may overlook the relationship between production location and vehicle value. Genuine awareness offers buyers the chance to make informed decisions, potentially increasing satisfaction and financial well-being regarding their purchases. Furthermore, knowledge about local sourcing and economies provides meaningful context to discussions about sustainability, reflecting how manufacturers like Toyota contribute to the communities in which they operate.
> The intersection of manufacturing, local economies, and consumer choice highlights a complex matrix and ensures intelligent discussions within automotive circles in the consumer realm.
Summary of Key Insights
- Global Footprint: Toyota's trucks are made in various strategic locations, including the United States in San Antonio and California, as well as Japan and Thailand.
- Economic Impact: Each plant contributes significantly to the local economy, providing jobs and fostering community relationships.
- Quality Assurance: Stringent quality control measures ensure that every vehicle reflects Toyota's commitment to excellence.
- Future Outlook: Innovations in manufacturing processes and a focus on sustainability highlight Toyota's proactive approach.
- Consumer Awareness: Recognizing where trucks are manufactured affects purchasing decisions, often leading to preferences for vehicles made domestically.
Final Thoughts on Toyota's Manufacturing Strategy
Toyota's manufacturing strategy excellently reconciles efficiency with local engagement. Their system reflects an awareness of the broader consequences of production choices. By strategically selecting manufacturing plant locations, Toyota adapts to regional needs while maintaining a consistent brand value across platforms. This flexibility enhances their capacity to respond to market demands swiftly, thus ensuring relevance in a rapidly changing automotive landscape. Moreover, the company's efforts in sustainability betray a consciousness that is leading many automotive brands toward a courteous relationship with nature.
Overall, as Toyota continues to evolve, it will likely sustain its dedication to both innovation and local engagement. For consumers and enthusiasts alike, understanding this canvas enriches conversations around Toyota's trucks, serving also as a benchmark for the industry.