Exploring Air Compressor Careers in the Automotive Sector
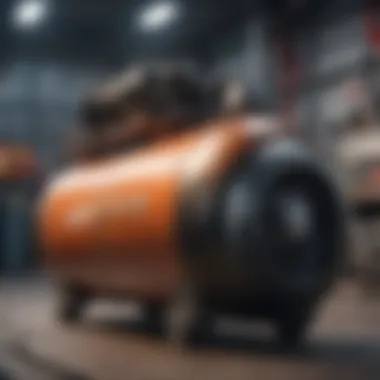
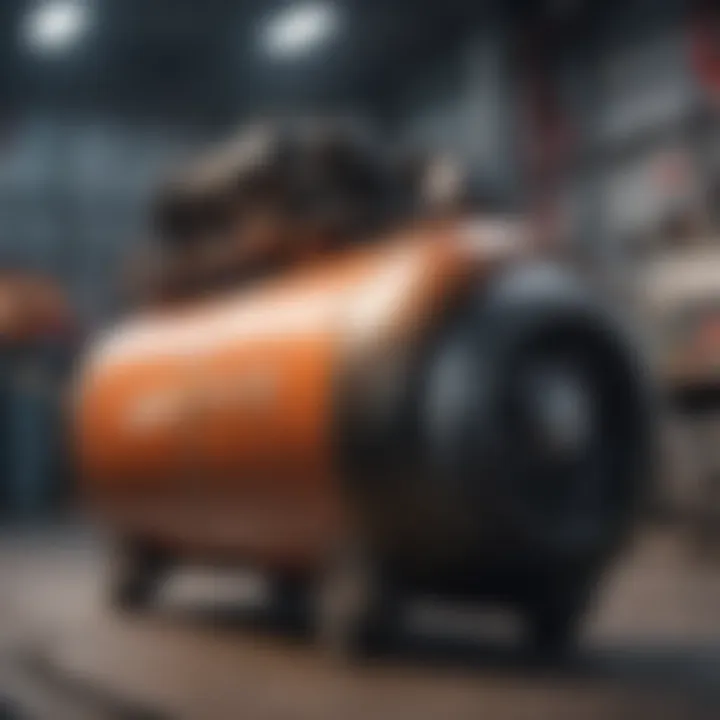
Intro
The automotive industry thrives on modern technology and plays a critical role in the economy. Within this elaborate system, air compressors facilitate various operations, such as diagnostics, assembly, and maintenance. Understanding air compressor jobs in this field unveils a realm of diverse responsibilities and opportunities. It is crucial to explore what positions are available, the vital skills needed, and the work environment.
Air compressors are essential in automotive processes. They compress air and make it suitable for different applications. These applications range from powering equipment to assisting in various automotive repairs. This article aims to discuss the different job roles associated with air compressors and their importance in automotive services and production lines.
As we dive into the sections ahead, we will cover specific job types, skills required, industry trends, and considerations for growth within the field. This comprehensive guide serves not only automotive professionals but also enthusiasts looking to understand the impact of air compressors in the industry.
Car Reviews
Overview of the Vehicle
Exploring how air compressors affect vehicle design and performance is valuable. Car models often encompass various systems relying on this technology. Air compressors provide compressed air needed for pneumatic tools used in assembly plants. Evaluating different brands of compressors, like Ingersoll Rand and Atlas Copco, reveals the capability each brings to the assembly process.
Performance Analysis
Examining how air compressors influence performance can illuminate their importance in automotive settings. For example, using specific types can reduce downtime during production. Their efficiency directly links to overall manufacturing effectiveness and vehicle functionality.
Design and Interior Features
The invisible yet impactful role of air compressors starts at the assembly line. Designers create vehicle features requiring accurate control of air pressure. Correct air delivery ensures components fit and operate as intended. This synergy showcases the vital role of compressors and associated jobs in design stages.
Safety Ratings and Specifications
When discussing the impact of air compressors on safety, maintenance comes to mind. They are used during inspections, repairs, and routine beauty jobs, directly influencing safety standards. Staff operating these tools need specified skills to function efficiently and responsibly.
Value for Money
Investing in high-quality air compressors impacts production quality. Setting up proper maintenance schedules and selecting essential equipment ultimately saves shop owners money and time in the long run.
Automotive Industry Trends
Emerging Technologies
Rapid shifts in technology affect air compressor systems. New innovations relating to energy efficiency, noise reduction, and versatility are essential trends. These factors spark new opportunities for skilled workers in the industry.
Changes in Consumer Preferences
Shifts in consumer preferences lead manufacturers to rethink their approach. Eco-friendliness ranks high on consumers' lists today, requiring more efficient air compressors to minimize energy use. Efficiency allows for better performance while addressing ecological concerns.
Sustainability and Eco-Friendly Practices
The automotive industry forwards efforts into sustainability. Companies look to align practices with environmental goals. Selecting energy-efficient compressors aligns well with these aspirations, complementing ongoing research into recycler-powered alternatives.
Future of Electric Vehicles
The rising interest in electric vehicles enhances competition, making it crucial for compressor technicians to adapt. As more EV brands enter the market, understanding compressor systems while integrating electric solutions becomes paramount.
Industry Challenges and Solutions
Factors impacting the automotive industry can pose challenges. Supply chain issues and economic fluctuations are pertinent. Addressing these hurdles lay the groundwork for discussing compressor jobs viability in evolving landscapes.
Epilogue
Air compressor roles in the automotive sector emerge as a critical yet often overlooked aspect. As vehicle technology constantly progresses, the importance of these positions grows.
For further learning, visit Wikipedia and Britannica. Active participation in online forums, such as Reddit, can also be beneficial for discussions. Strong careers and sectors depend on these functional roles that support rapid automotive advancements.
Intro to Air Compressor Jobs
Understanding air compressor jobs is crucial in the automotive industry, as these roles directly involve the production, maintenance, and operation of essential equipment. Air compressors are integral to various processes in automotive manufacturing and repair. Moreover, the nature of these jobs goes beyond technical tasks and incorporates elements like efficiency improvements, safety considerations, and economic contributions.
Defining Air Compressors
Air compressors are devices that increase the pressure of air by reducing its volume. They convert power into potential energy stored in pressurized air. This process plays a vital role in many applications, particularly in the automotive sector.
The basic function of an air compressor involves drawing in ambient air, compressing it, and then storing it for later use. There are several types, including reciprocating, rotary screw, and centrifugal compressors. Each type has unique features and is suited for different industrial processes. An understanding of these various types helps in understanding their use in the automotive landscape.
Importance of Air Compressors in Automotive
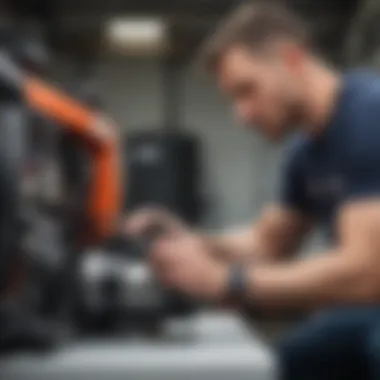
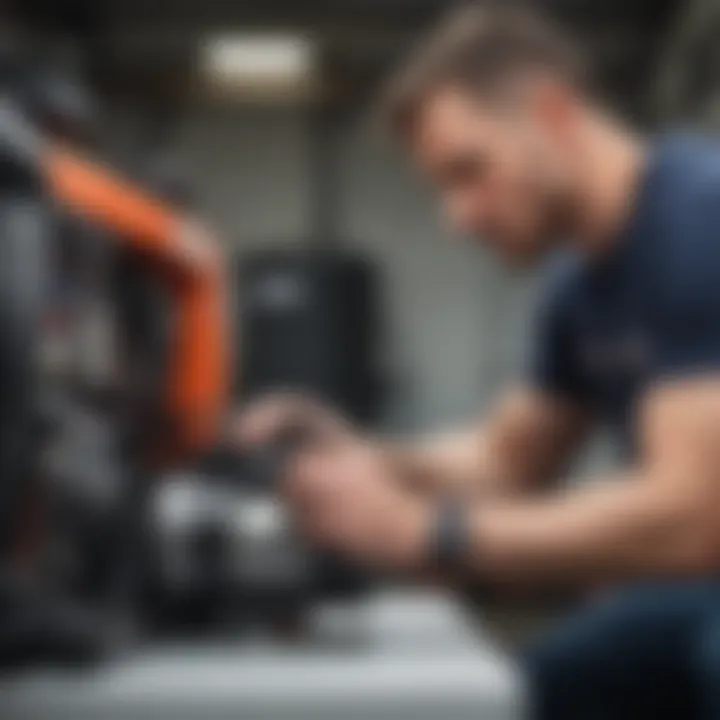
Air compressors hold significant importance in automotive operations for several reasons. Firstly, they are crucial for operating pneumatic tools like impact wrenches and spray guns. This optimizes efficiency in tasks such as assembly, painting, and repair work.
Secondly, air compressors ensure that production processes maintain required pressure levels for various applications—effectively enhancing the overall workflow. In manufacturing facilities, compressed air systems packaging, material handling, and more.
Additionally, the automotive industry is continuously focusing on lowering operational costs and maximizing productivity. Air compressors contribute to these goals while supporting safety measures. For instance, they provide a clean source of energy in comparison to fuels. This transition towards cleaner energy resonates with the ongoing industrial revolution.
Types of Jobs in Air Compressor Operations
Air compressors play a critical role in the automotive industry. Thier reliability affects everything from vehicle assembly to servicing. The types of jobs focused on air compressor operations are essential for maintaining optimal performance and efficiency in automotive processes. Understanding these roles can shed light on career paths and their significance in an ever-evolving industry.
Maintenance Technicians
Maintenance technicians are pivotal in ensuring that air compressors operate without hitches. Their role involves regular inspections, troubleshooting mechanical issues, and servicing equipment to prolong its lifespan. These technicians possess mechanical skills and often have training in electrical systems and diagnostics.
Key Responsibilities of Maintenance Technicians:
- Routine Check-Ups: Performing inspections to ensure compliance with safety standards.
- Diagnostic Testing: Using specialized tools to identify and resolve issues swiftly.
- Preventative Actions: Implementing strategies to minimize downtime.
Effective maintenance prevents costly repairs down the line and guarantees the reliability of compressors used in manufacturing or repair environments. Technicians might specialize in well-known brands such as Ingersoll Rand or Atlas Copco, making their expertise even more focused.
Production Operators
Production operators are another crucial job category. Their daily responsibilities include operating and monitoring air compressors within a production facility. These operators ensure that compressors provide the required air pressure and volume needed for diverse operations, such as spray painting or pneumatic tool usage.
Essential Tasks for Production Operators:
- Monitoring Systems: Keeping an eye on gauges and indicators to maintain optimal airflow.
- Adjusting Settings: Modifying controls based on specific requirements of the task at hand.
- Documenting Operations: Keeping records of performance metrics and operational issues for further analysis.
Efficient production operators are often versed in the latest technology and trends, allowing them to maximize compressor output while reducing waste.
Sales and Technical Support
Sales and technical support representatives serve a different but essential purpose in the realm of air compressor jobs. Their focus is to inform customers about various compressor options and technical capabilities. Knowledge of different air compressor systems is vital, as is the ability to diagnose problems and offer solutions.
Functions of Sales and Technical Support:
- Client Consultation: Understanding customer needs and suggesting appropriate products.
- Technical Training: Providing customers with knowledge on equipment operation.
- After-Sales Service: Assisting clients with any post-purchase challenges and maintenance-scheduling issues.
Professionals in these roles are often regarded as the bridge between the manufacturer and the end-user, ensuring efficient communication and a smooth integration of air compressors within the customer's operational framework. Understanding market trends is critical, specifically in relation to customer demands and environmental regulations that affect specifications and usage.
Today's automotive industry demands skilled employees who can adapt to rapid changes in technology and practices. Understanding varied job roles in air compressor operations lays the foundation for significant career growth and stability.
Essential Skills for Air Compressor Roles
A particular focus on essential skills for air compressor roles facilitates the understanding of what makes a good candidate in this field. Competence in these skills can tremendously enhance one's performance, career outlook, and overall effectiveness in various roles that involve air compressors within the automotive industry.
Technical Knowledge
Technical knowledge is a cornerstone skill for anyone working with air compressors. This includes a solid grasp of mechanical systems, hydraulics, and pneumatics. Knowing how an air compressor functions, its various components, and their interrelations allows professionals to troubleshoot problems efficiently and perform routine maintenance tasks. Technicians require insights into the different types of compressors—like reciprocating, rotary screw, and centrifugal—as each has distinct operating principles and maintenance needs. Moreover, understanding the specifications outlined in technical documentation can aid in the selection of the correct compressor for specific applications.
One cannot underestimate the potential job risks linked to inadequate knowledge. For instance, failures due to miscalculations or poor understanding of compressor load limits could lead to safety incidents and, consequently, significant downtime. Familiarity with compressors' capacity, energy efficiency ratings, and environmental impact plays a vital role in fostering sustainable industry practices and improving organizational efficiencies.
Problem-Solving Skills
Problem-solving is crucial in air compressor roles, particularly when unanticipated issues arise. Technicians often face urgent mechanical failures or fluctuations in air pressure that hinder production. Having strong problem-solving skills allows these professionals to quickly identify problems and think critically about solutions. This might involve temporary fixes or long-term strategies to avoid repetitive issues, all while maintaining the effectiveness of operations.
It is essential to employ systematic approaches to problem-solving. Problem diagnosis techniques mainly include conducting root cause analysis, implementing effective solutions, and testing the outcome of those solutions. Individuals should articulate issues clearly, propose efficient solutions, and anticipate potential repercussions of their decisions. Thus, fostering an environment of continuous improvement and adaptability.
Safety Protocols
The significance of adhering to stringent safety protocols in air compressor roles cannot be overstated. Safety operates as a critical element, as compressed air operates under high pressure, which can pose significant hazards. Familiarity with safety regulations and industry standards ensures that all computations and operations remain within the safe operational limits.
Essential safety standards include wearing proper personal protective equipment (PPE) like goggles, gloves, and hearing protection when working with heavy machinery. A daily check on hoses, fittings, and safety valves also goes a long way in mitigating risks of uncontrolled air release or equipment failure. Training sessions that focus on safety must become an ongoing process, regularly updated as technology evolves and new regulations emerge. Creating a culture of safety not only protects employees but also enhances productivity as confident, knowledgeable workers capable of following procedures aid in mitigating incidents.
Work Environment and Conditions
Understanding the work environment and conditions in air compressor jobs is crucial for several reasons. Automotive professionals are often exposed to different settings that demand various levels of physicality and technical expertise. This section will explore the distinct environments where these compressors are utilized, along with considerations that affect the safety and effectiveness of the workers involved.
Industrial Settings
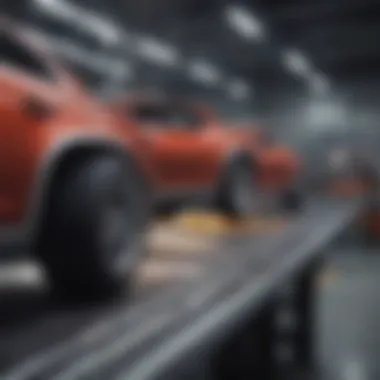
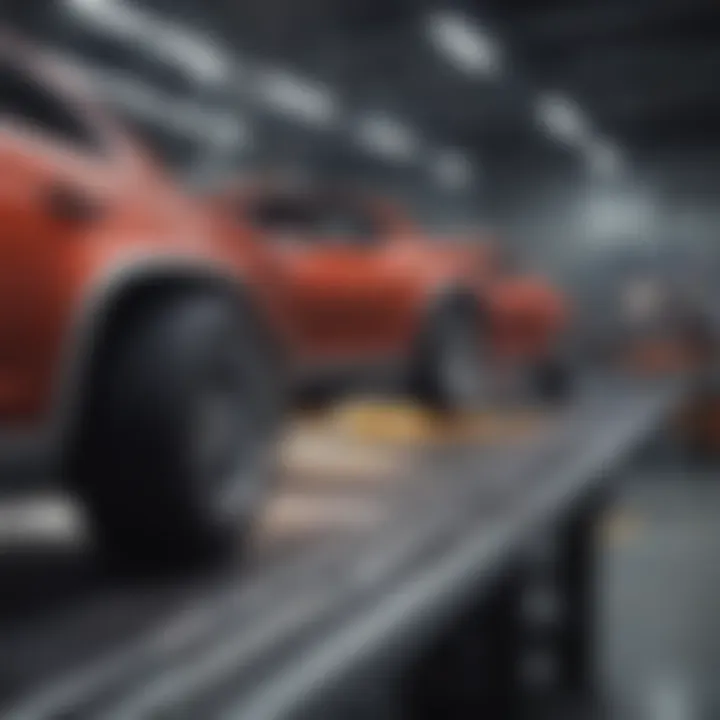
Jobs related to air compressors are often situated in industrial settings like manufacturing plants, assembly lines, and automotive repair shops. These locations are equipped with heavy machinery and tools that produce high levels of noise and potentially hazardous conditions. Therefore, it is essential for workers to have strict adherence to safety protocols.
Air compressors are found in these environments primarily because they power various tools and machinery that require high-pressure air, helping automate processes that increase efficiency. Equally, working in these environments demands physical ability, familiarity with complex systems, and knowledge of mechanical operations. Proper ventilation is also a critical consideration, as industrial settings may have airborne dust or vapors from other machine operations.
Some key factors influencers for professionals in industrial settings include:
- Noise Levels: These environments often expose employees to significant auditory stimuli, necessitating the use of hearing protection.
- Spacing: For safe operation, keeping an organized and clutter-free workspace avoids accidents or interferences during maintenance.
- Temperature Control: Extreme temperatures may occur in certain facilities, stressing the need for appropriate personal protective equipment (PPE) and hydration.
Field Work vs.
Workshop Work
Contrasting with industrial settings, field work typically involves onsite tasks that could be at customer locations, vehicles, or specialized service centers. In these situations, technicians may encounter diverse environments, which vary in difficulty and unexpected conditions. For instance, weather can impact a technician's ability to perform effectively outdoors.
Workshop work, on the other hand, usually provides a more controlled environment in terms of safety and tools available. In a workshop, air compressor jobs focus not just on repairs but also involve routine maintenance and testing of various automotive systems in a secure location.
Key Comparisons Include:
- Nature of Work: Fieldwork demands flexibility and problem-solving skills, as technicians must adjust to varying circumstances, while workshop work typically comprises structured tasks with a predictable flow.
- Safety Challenges: Workshops can offer higher control towards safety compared to fieldwork, where unforeseen events can increase risk.
- Equipment Access: Typically in a workshop, tools are readily available, whereas, in the field, professionals may work with limited equipment suited for specific tasks.
Ultimately, understanding work environments and conditions will empower individuals to navigate their careers in air compressor jobs efficiently. Their choice of settings will have lasting impacts on professional growth and personal safety.
Safety Considerations in Air Compressor Jobs
Air compressors are integral to the automotive sector, enhancing efficacy and productivity. However, safety is paramount when working around these powerful machines. The unique challenges and hazards they present demand a well-thought-out approach to workplace safety. Recognizing the importance of safety considered in air compressor jobs is vital, as it helps workers comprehend the risks and implement measures to mitigate potential accidents. Adhering to safety protocols can prevent injuries and entrench a culture of responsibility among employees.
Workplace Safety Standards
Ensuring a safe work environment in air compressor operations involves compliance with established workplace safety standards. The Occupational Safety and Health Administration (OSHA) provides guidelines to manage the inherent risks that come with the use of compressed air systems. These standards cover various aspects, including machine guarding, noise exposure, and proper ventilation. Employees in this field should regularly undergo safety training to stay informed and adept at recognizing hazards.
Some specific workplace safety elements to be familiar with include:
- Risk Assessments: Periodic evaluation of potential hazards related to air compressor environments is necessary. This helps in adopting preventive measures, significantly reducing the risk of accidents.
- Emergency Response Plans: Having clear emergency protocols in place contributes to a quick response during unforeseen accidents. Structured drills should familiarize all employees with these actions.
- Regular Inspections and Maintenance: Unsatisfactory maintenance leads to unforeseen malfunctions that may risk safety. Establish a routine to inspect air compressors and the surrounding operational area.
Safe practices not only protect workers but also contribute to the efficient operation of air compressors. Sustaining safety standards reflects a commitment to both human resources and operational excellence.
Personal Protective Equipment (PPE)
Using proper Personal Protective Equipment (PPE) is essential for those working with air compressors. With the unpredictable nature of damages and injuries, equipping staff with reliable PPE creates a safer environment. Here are the most common types of PPE necessary:
- Hearing Protection: Air compressors can exceed hazardous noise levels. Earplugs or earmuffs guard against hearing loss.
- Eye Protection: Safety goggles or face shields protect against flying debris resulting from compressor operations.
- Respiratory Protection: When working in areas where air quality may be compromised, wearing respirators shields against inhalation of harmful substances.
- Gloves and Safety Footwear: Protective gloves provide grip and prevent cuts, while reinforced safety footwear protects from heavy equipment hazards.
Employers should also conduct regular training on the importance of wearing PPE correctly and consistently. It is the responsibility of both employers and employees to prioritize safety for a secure working experience in air compressor jobs. Failing to do so not only endangers individuals but jeopardizes the entire operational integrity.
Career Progression in Air Compressor Jobs
Career progression within air compressor jobs in the automotive industry is not only vital for personal development, but also plays a crucial role in the overall efficiency and innovation of the sector. As technology evolves, professionals who work with air compressors must adapt and expand their skill sets. They can benefit from various opportunities as they progress through their careers, which enhances not just their competencies but also the efficacy of the automotive operations.
Working within air compressor jobs, individuals start at different stages. These roles often provide hands-on experience, developing fundamental skills relevant to larger operations. However, as employees progress, they find opportunities that offer greater responsibilities and challenges, helping them evolve as industry professionals.
Entry-Level Opportunities
New entrants often begin their careers with several available entry-level positions, such as air compressor technicians or operators. These roles are crucial, as they encompass basic operational practices and routine maintenance.
In entry-level roles, individuals will likely focus on tasks such as:
- Performing routine checks on air compressors.
- Assisting in maintenance and repairs.
- Learning the safety protocols essential in the workplace.
- Familiarizing themselves with automotive equipment that relies on compressed air.
Entering these positions lays a solid foundation for further study and exploration in the automotive environment. Understanding the daily operations around air compressors equips new technicians with necessary skills to advance in various capacities.
Advanced Career Paths
Advanced roles within air compressor jobs often involve positions such as systems engineers, supervisors or even technical consultants. At this juncture, practitioners begin specializing in more complex applications of air compressors in the automotive industry.
In advanced roles, professionals are responsible for:
- Designing and optimizing systems that utilize compressed air.
- Leading project teams focused on new technologies.
- Managing departments that ensure compliance with safety and environmental standards.
- Providing expertise in pneumatic systems that integrate with automotive processes.
The ability to navigate these advanced roles often comes from experience and continuous education. Professionals may pursue certifications or attend classes to refine their skills in advanced mechanics, which directly influences their job performance and advancement.
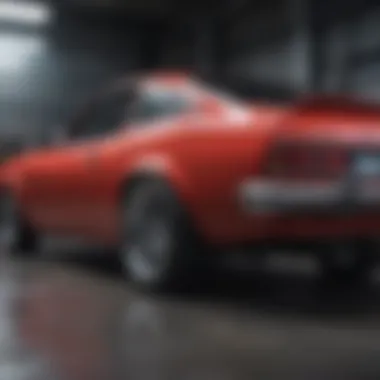
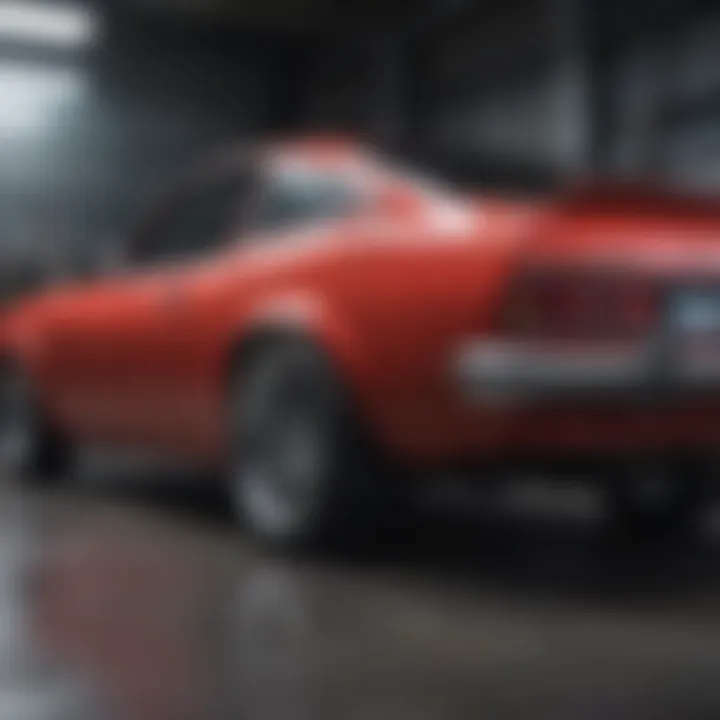
It is essential to keep in mind that the journey within air compressor jobs can vary significantly based on an individual’s eagerness to learn and adapt. Those who show initiative and actively seek opportunities for growth will likely find a more rewarding career path and potentially gain roles that have significant impact on the automotive industry.
Impact of Technology on Air Compressor Jobs
The impact of technology on air compressor jobs in the automotive industry is profound, shaping the way tasks are performed and redefining equipment standards. The integration of technology brings efficiencies, improves reliability, and enhances overall productivity. By understanding how these advancements affect various roles, professionals can better navigate their careers.
Automation and Robotics
Automation plays a vital role in modernizing air compressor jobs. Automation reduces manual labor, allowing machines to perform repetitive, labor-intensive tasks. For instance, automated controls often monitor air levels and maintain consistency in pressure. Here's a deeper look into some key aspects of automation in air compressor jobs:
- Increased Production Efficiency: Machines equipped with automated technology operate at higher speeds and with greater precision than human operators. This boosts production levels in automotive workshops.
- Reduced Human Error: Automated processes minimize the chances of errors that can occur in manual operations. Trained professionals can focus on more complex challenges rather than mundane tasks.
- Cost-Effective Operation: While initial investments in technology can be high, reducing labor costs over time is one of the long-term benefits. Continued use and reliance on automation lead to operational efficiencies and therefore savings.
Robotic Applications in Maintenance
Robotics in maintenance tasks can enhance the upkeep of air compressors. Certain robotic systems are now being deployed for routine checks, reducing the need for direct human involvement in potentially hazardous areas. Such advancements in technology are crucial for maintaining safety and regulation standards in automotive environments.
Emerging Technologies
With disruptions across industries, emerging technologies are also making their mark on air compressors. Keeping institutions updated on the latest technologies ensures that automotive entities can adapt effectively. Some emerging trends include:
- Smart Compressors: IoT-enabled air compressors use sensors to collect data on performance. This allows technicians to monitor equipment condition, leading to proactive maintenance.
- Energy Efficiency Improvements: Technologies are focusing more on energy-efficient compressor designs. This decrease in energy consumption aligns with environmental regulations and helps companies reduce their carbon footprint.
- Remote Monitoring Systems: Management systems enable remote diagnostics of air compressors. This not only helps in timely identification of troubles but also decreases downtime significantly.
Understanding and integrating these emerging technologies will advance equipment reliability and operational efficiency, thus contributing positively to job roles related to air compression.rud
Adopting advanced tech not only enhances productivity but also prepares professionals for a competitive job market.
The landscape of air compressor jobs continues to evolve as technology progresses. Professionals in the automotive industry must stay informed about these changes to remain relevant and skilled in their roles.
Industry Trends Affecting Air Compressor Employment
Understanding the industry trends affecting air compressor employment is essential for anyone involved in this niche sector of the automotive industry. These trends provide insights into where the workforce is headed, responding to both technological innovations and fluctuations in market demands. For example, staying aware of the shifts brings a better understanding of job security and career advancement opportunities. As companies adjust to meet ever-evolving demands, it is crucial to know how the shifts can affect hiring practices and the skill sets sought after by employers.
Current Market Demand
The current market demand for air compressor professionals directly relates to the broader automotive industry's health. With a focus on efficiency, manufacturers are investing more in automation and upgrades to existing systems. This growing need translates into numerous job roles that require expertise in air compressor technology. Factors that contribute to this dynamic demand include an increase in vehicle production and outdated existing systems in need of modernization.
- Rapid Expansion of Electric Vehicles: The rise of electric vehicles (EVs) has created a demand for facilities equipped with compliant air compressor systems for maintenance and production needs.
- Shift Towards Sustainable Practices: As companies transition to more eco-friendly practices, the push for energy-efficient compressors grows. This necessitates workers skilled in optimizing machinery for lower emissions.
Due to these factors, many employers are actively seeking candidates with specific certifications and background experience in air compressor roles. Being knowledgeable about the current market allows professionals to position themselves accordingly.
Environmental Regulations
Changing environmental regulations are another integral factor that impacts employment in the air compressor sector. The industry faces stringent laws concerning emissions and energy use. Compliance with these regulations not only leads to improved operational practices but also drives the demand for skilled workers who understand these specific requirements.
- Higher Compliance Standards: Regulations necessitate the implementation of technology that reduces environmental impacts. This creates a demand for individuals who can integrate these new systems efficiently.
- Sustainability Goals of Companies: Organizations are emphasizing sustainability, reflecting in policies that influence operations and hiring practices.
Companies often prefer to hire professionals well-versed in compliance and who can stay abreast of changes in regulations. Thus, individuals equipped with such expertise may gain a competitive edge in the job market.
The shifting landscape of industry trends mirrors the automotive sector's broader advancements and can pave the way for a prosperous career in air compressors.
For a more comprehensive understanding of background on these poorötanta Market Values or regulatory contexts, you may refer to resources like Wikipedia or community discussions on Reddit.
Resources for Aspiring Professionals
Understanding the importance of resources for aspiring professionals in air compressor-related jobs within the automotive industry is crucial. Specialized tools, like air compressors, play an extensive role in vehicular production and repair. Therefore, acquiring proper knowledge and obtaining the needed qualifications are integral for individuals looking to enter or advance in this field.
Various resources offer paths to develop skills and gain necessary knowledge. Engage with certification programs that focus on technical expertise, which can significantly enhance one's employability and pave the way for career growth. Networking opportunities also arise through professional associations, providing insights and connections to industry leaders and peers. Leveraging these resources can help potential candidates stay informed of market trends and technological innovations.
Finale
The conclusion serves as an essential summary in this detailed overview of air compressor jobs within the automotive industry. It allows us to encapsulate critical insights while projecting future potential. A well-constructed conclusion reinforces the significance of understanding the evolving role of air compressors.
In examining air compressor jobs, we discussed various niches, the necessary skills, and career opportunities. These elements lead to a form of clarity about operational efficiency in the automotive sector. As technology advances and creates shifts in the job landscape, staying informed about these roles is crucial for aspiring professionals.
A tagline could be: Navigating to success: Equal parts determination and knowledge creates the best opportunities in air compressor roles.
Recap of Key Points
- Air Compressors in Automotive: Fundamental to processes in maintenance and production.
- Job Types Explored: Various job roles like maintenance technicians, operators, and support staff illustrate the diversity.
- Essential Skills: Knowledge in safety, technical realms, and problem-solving is indispensable.
- Work Environments: Differentiation between fieldwork and industrial settings provides critical understanding for candidates.
- Safety Considerations: Emphasis on qualifying as essential for working responsibly in these roles.
- Career Pathways: Clear progression pathways are visible for those willing to seek them out, including certifications.
- Technological Influence: Today’s emerging technology shapes the future relevance of these roles in automotive.
- Industry Trends: Environmental regulations and market demand drive adaptation in job roles.
- Professional Resources: Various certifications augment career prospects and skillsets important for advancement.
Future Outlook for Air Compressor Jobs
As we gaze into the near future, the prospects for air compressor specialties remain promising. The shift towards automation and sophisticated equipment means that professionals will need ongoing training and adaptability. Employers are likely to continue favoring candidates with a solid technical background, as modern skills integration becomes crucial.
- Emerging Jobs: New positions may develop as electric and hybrid vehicle production increases.
- Regulatory Awareness: Keeping abreast with environmental standards adds a layer of importance to these jobs going forward.
- Skills Evolution: Continuous development and recognition of alternative energy uses in air compression can elevate career profiles.
- Market Demand: Steady expansion in the automotive sector implies sustained requirements for air compressor roles.
Those who engage with these dynamics will likely possess competitive edges in the job market. Both challenges and opportunities convery an ongoing fascination with this critical field, driving both professionals and companies toward future innovations and solutions.