Tesla Production Dynamics: Strategies and Innovations
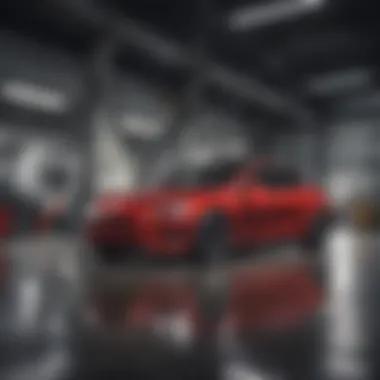
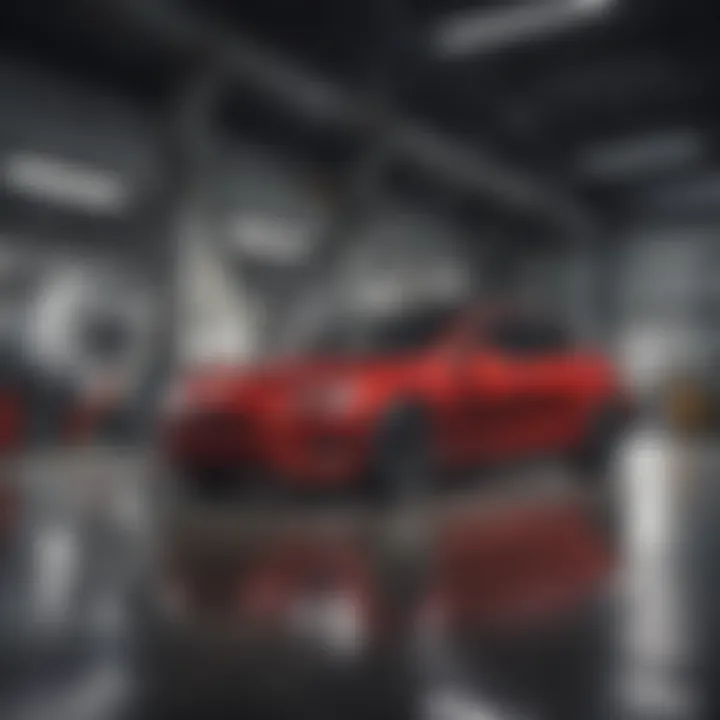
Intro
Tesla's production dynamics play a crucial role in shaping the landscape of the automotive industry. This article dives deep into the intricate workings of Tesla's manufacturing processes, offering insights into strategies, technology, and supply chain management. As the electric vehicle market continues to grow, understanding how Tesla maintains a balance between innovation and efficiency becomes increasingly important for both enthusiasts and industry professionals.
Through a detailed analysis, we will explore the evolution of Tesla's manufacturing capabilities and how its Gigafactories fit into the larger picture. Moreover, we will assess how external factors, such as global market conditions, impact Tesla's operations.
By examining these aspects, we aim to provide a comprehensive guide that not only highlights key points of discussion but also illustrates their relevance within the industry. This exploration serves to equip readers with a better understanding of where Tesla stands today and its trajectory for the future.
Overview of Tesla's Manufacturing Philosophy
Tesla's manufacturing philosophy is a cornerstone of its identity in the automotive industry. The approach taken by Tesla is not merely about building electric vehicles; it is a radical rethinking of production dynamics and efficiency. Understanding this philosophy provides valuable insights into Tesla's successes and challenges, as well as its broader impact on the automotive landscape.
Preface to Tesla's Approach
Tesla’s approach to manufacturing centers on a blend of innovation and vertical integration. From the onset, the company aimed to disrupt traditional automotive production models. This is significant because it not only focuses on meeting consumer demand but also emphasizes sustainability and scalability. Additionally, Tesla integrates advanced technologies at various stages of production, including design, assembly, and supply chain management. Such integration enhances quality control and streamlines operations.
The philosophy extends beyond mere assembly lines. It incorporates principles of agility, allowing Tesla to swiftly adapt to changes in market demand. This responsiveness is critical in an industry where consumer preferences shift rapidly. By utilizing technology-driven solutions, Tesla aims to reduce waste and improve energy efficiency, making it a leader in eco-friendly practices within the automotive sector.
Key Manufacturing Principles
Tesla's manufacturing principles can be summarized into several key categories that define its production strategy and efficiency:
- Automation: Tesla employs advanced robotics and automation systems in its factories, aiming to enhance productivity while lowering labor costs. The use of automated systems allows for consistent quality and faster production cycles.
- Vertical Integration: By producing many components in-house, Tesla minimizes reliance on external suppliers. This strategy not only increases control over quality but also reduces supply chain risks.
- Lean Manufacturing: The company adopts lean principles to eliminate waste in production processes. This approach emphasizes continuous improvement and responsiveness, ultimately leading to higher efficiency.
- Sustainable Practices: From battery production to vehicle assembly, sustainability is a guiding principle. Tesla prioritizes materials and processes that reduce environmental impact, aligning with its mission to accelerate the world’s transition to sustainable energy.
- Real-Time Data Utilization: Tesla utilizes real-time data to monitor production processes. This practice enables quick adjustments to improve efficiency and respond to potential issues before they escalate.
These key principles not only drive Tesla's production dynamics but also set benchmarks for the industry. They exemplify a forward-thinking mindset that prioritizes innovation while addressing contemporary challenges in manufacturing.
Evolution of Tesla's Production Techniques
The evolution of Tesla's production techniques has greatly influenced its position in the automotive industry. This topic is not only significant for understanding how Tesla has risen to be a leader in the electric vehicle space, but it also showcases the innovative strategies that have reshaped modern manufacturing practices. The advancements in Tesla's production processes illuminate their ability to respond to consumer demand, optimize resources, and enhance product quality.
Key factors in the evolution of Tesla’s production methods include:
- Innovation and Flexibility: Tesla has incorporated innovative production techniques enabling them to adapt quickly to changing market conditions.
- Efficiency Improvements: Continuous updates in manufacturing processes boost efficiency and reduce costs, which are crucial for sustainability in the competitive automotive market.
- Integration of Technology: By integrating smart technologies, Tesla has optimized production workflows and minimized waste.
In essence, understanding the evolution of Tesla’s production techniques unveils how the company has navigated challenges and strategically positioned itself for future growth in the automotive sector.
Early Production Models
Tesla’s early production models, starting with the Roadster in 2008, were significant learning experiences. These models laid the groundwork for Tesla's understanding of electric vehicle production. The company had to confront various obstacles including:
- Limited Manufacturing Scale: Initial production capacities were low due to limited resources.
- Supply Chain Constraints: Establishing a reliable supply chain for specialized electric components proved to be challenging.
- Quality Control Issues: Ensuring consistent quality during early production was difficult, leading to operational setbacks.
Despite these challenges, the Roadster established Tesla’s reputation and provided essential insights into future vehicle designs and production techniques.
Transition to Modern Manufacturing
As Tesla transitioned to modern manufacturing, it embraced advanced techniques that would redefine automotive production. This transition involved several critical improvements:
- Automation: The introduction of automated processes was essential. This allowed Tesla to scale operations while maintaining quality control. Robotics became a vital component, particularly in the assembly stage.
- Gigafactory Development: The establishment of Gigafactories marked a significant shift. These facilities enhanced production capabilities, enabling mass manufacturing of battery packs and electric vehicle components, contributing to lower costs.
- Lean Manufacturing Practices: Tesla adopted lean production principles that focus on minimizing waste while maximizing productivity. This approach supports a streamlined production flow.
- Collaborations with Suppliers: By fostering strong relationships with suppliers, Tesla ensured a more robust supply chain, which is vital for consistent production.
The transition to these modern techniques has equipped Tesla to face growing market demands and to respond flexibly to consumer needs. The impact on production rates and vehicle quality has been considerable, positioning Tesla as a pioneer in efficient and effective electric vehicle manufacturing.
"Through continual refinement of production methods, Tesla has not only improved its efficiency but also challenged traditional automotive manufacturing models."
Embracing technological advancements and reevaluating production strategies has allowed Tesla to maintain its leadership in the ever-evolving automotive landscape.
The Gigafactory Concept
The Gigafactory concept plays a crucial role in Tesla's strategy for production and supply chain efficiency. This innovative manufacturing approach aims to significantly reduce battery costs and enhance production capabilities. The Gigafactory allows Tesla to scale up battery production in a single location, which is essential as electric vehicle demand grows globally. It is also a key element of Tesla’s commitment to sustainable energy through vertical integration of battery production and assembly under one roof.
Gigafactory Locations and Capacities
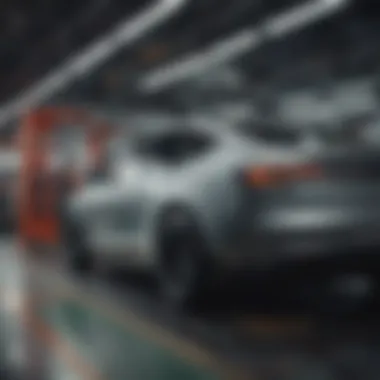
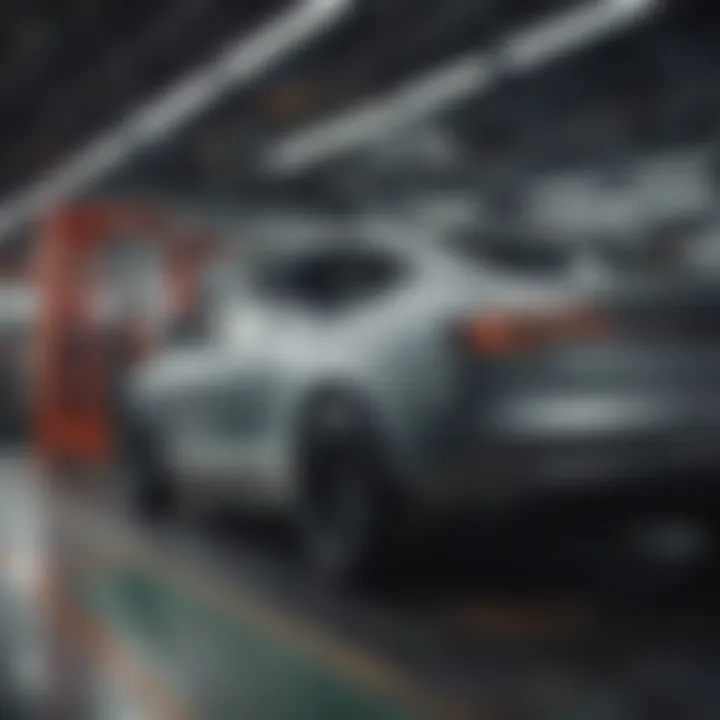
Tesla has established Gigafactories in strategic locations around the world to optimize production and logistics. Some of the most notable are:
- Gigafactory 1 (Nevada, USA): This was Tesla's first Gigafactory, primarily focused on lithium-ion battery production. Its planned capacity aims to produce enough batteries to power 500,000 electric vehicles annually.
- Gigafactory 2 (New York, USA): Though primarily focusing on solar products, this facility supports Tesla's overall energy products by manufacturing solar panels and solar roofs.
- Gigafactory 3 (Shanghai, China): Opened in 2019, this factory allows Tesla to produce vehicles for the Asian markets, significantly increasing its production capacity. It enables faster deliveries and reduced logistical costs.
- Gigafactory Berlin (Germany): This facility is set to manufacture the Model Y and battery cells, aiming to serve the European market efficiently.
- Gigafactory Texas (USA): This site is also crucial for producing the Model Y and Cybertruck. Its vast size is intended to meet future demand.
Each Gigafactory is engineered with ambitious production goals, and their strategic placement is designed to minimize transportation costs and time, thus enhancing Tesla's responsiveness to market conditions.
Impact on Production Output
The establishment of Gigafactories has led to a profound impact on Tesla's overall production output. By concentrating resources and manufacturing capabilities in one location, Tesla has managed to increase production speed and efficiency. For instance:
- Economies of Scale: The large-scale production allows Tesla to lower battery costs significantly, which is critical in making electric vehicles more affordable to consumers.
- Streamlined Operations: By integrating various production stages, Tesla reduces transit time for materials and components. This lean manufacturing approach maximizes throughput and minimizes waste.
- Enhanced Research and Development: Centralizing production at the Gigafactories facilitates close collaboration among engineering and production teams, accelerating innovation and improvements in manufacturing processes.
- Adaptability: The modular structure of these factories also allows Tesla to quickly adapt to changes in market demand and technology.
The overall effect is a robust supply chain that enhances Tesla's ability to scale production and meet global electric vehicle demand efficiently.
"Gigafactories represent a significant shift in automotive manufacturing, positioning Tesla to lead in the electrification of transport while maintaining cost-efficiency."
With this approach, Tesla not only boosts its production capabilities but also reinforces its vision of sustainable energy consumption.
Technological Innovations in Production
Technological innovations play a crucial role in Tesla's production efficiency and product quality. These advances enable the company to maintain its competitive edge in the automotive sector. Through automation and material science advancements, Tesla not only streamlines its production processes but also enhances overall performance. Understanding these innovations provides valuable insights into Tesla's manufacturing strategy and how it approaches changes in a rapidly-evolving market.
Automation in Manufacturing
Automation has changed significantly how Tesla operates its factories. By employing advanced robotics, the company reduces manual labor robustly. Machines can perform repetitive tasks with precision and speed that far exceeds human capability. For instance, automated systems handle welding, painting, and assembly tasks. This technology minimizes errors and improves production consistency.
Furthermore, automation increases production rates. With robots working continuously, Tesla can achieve higher outputs in less time. As a result, meeting market demand becomes more feasible. This is particularly important during periods of high interest in new models or features. However, automation does come with considerations. It mandates continuous investment in technology and training for human workers who manage these systems.
- Benefits of Automation:
- Increased production speed.
- Enhanced precision in manufacturing processes.
- Reduced labor costs over time.
- Improved consistency across production runs.
Despite these advantages, leaning heavily on automation poses risks. A system malfunction or software failure can halt production, leading to significant delays. Thus, Tesla must maintain a balance between automation and human oversight.
Material Science Advancements
Material science plays an essential role in improving vehicle performance. Tesla continuously seeks new materials to enhance durability and efficiency. Lightweight composites and stronger alloys are examples of innovations used in vehicle construction. The choice of materials impacts everything from energy consumption to safety ratings.
Advances in battery technology, particularly, mark a significant area of focus. Improvements in lithium-ion batteries allow for longer ranges and shorter charging times. Tesla's research into alternative materials, such as solid-state batteries, holds promise for even greater efficiencies in the future. The goal is not just to make better batteries but to make them in a more sustainable manner.
Moreover, understanding the properties of materials helps in designing systems that can withstand various stresses. For instance, the use of high-strength steel in certain areas of the vehicle provides protection without adding unnecessary weight. This impacts both handling and efficiency positively.
- Key Focus Areas in Material Science:
- Development of lightweight and stronger materials.
- Innovations in battery technology for improved performance.
- Sustainable sourcing of materials to reduce environmental impact.
"Innovations in material science are fundamental to Tesla's mission to accelerate the world's transition to sustainable energy."
In summary, technological innovations in production, through automation and advancements in material science, underscore Tesla's commitment to efficiency and quality. These factors not only enhance the immediate production capabilities but also position the company favorably in the long-term automotive landscape.
Supply Chain Management Challenges
The significance of supply chain management in Tesla's production dynamics cannot be overlooked. The efficient movement of materials and components is central to maintaining Tesla's production targets and ensuring the timely delivery of vehicles. Considering the global landscape, Tesla faces several challenges related to supply chain management, which can impact costs, production efficiency, and ultimately, market competitiveness.
A robust supply chain can lead to numerous benefits such as cost savings, improved speed to market, and increased agility in responding to consumer demands. However, the complexities within supply chains, especially in the automotive industry, can introduce risks. This requires constant evaluation and adaptation of strategies to manage these supply chain intricacies effectively.
Sourcing Raw Materials
Sourcing raw materials is critical in Tesla's supply chain strategy. The company uses a variety of materials, including lithium, cobalt, aluminum, and nickel, which are essential for battery production and other components. The extraction and processing of these materials often involve geopolitical factors and environmental considerations.
Tesla places emphasis on establishing strong supplier relationships to mitigate risks associated with raw material acquisition. Evaluating potential partners based on their sustainability practices and reliability ensures a steady flow of necessary inputs. Additionally, the recent constraints in the mining sector have pressed Tesla to seek alternative sources or substitutes, enhancing long-term material availability.
- Key considerations in sourcing include:
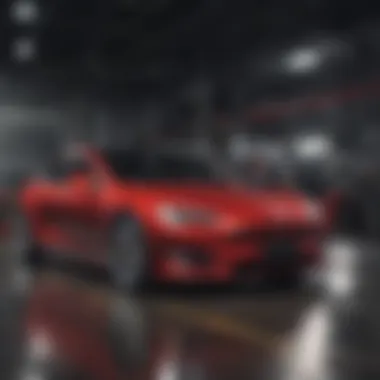
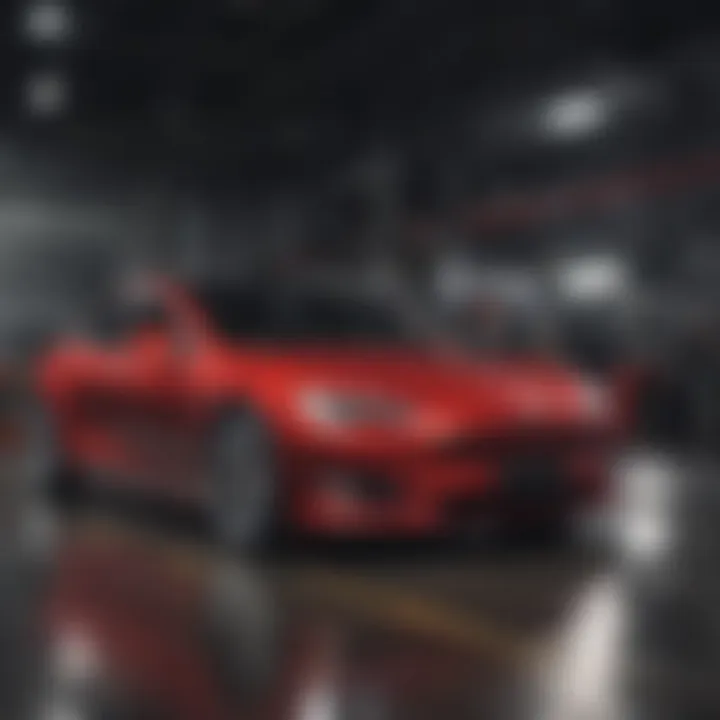
- Supplier reliability
- Cost fluctuations
- Environmental impact
All of these factors must be weighed for effective planning and risk management in Tesla's production cycle.
Logistical Complexities
Logistical complexities pose another significant challenge in Tesla's supply chain management. The intricate web of transporting materials, components, and finished vehicles requires meticulous planning and execution. Tesla's global manufacturing footprint compounds these logistical demands, as parts may come from various locations worldwide.
Efficient logistics is vital for minimizing delays and ensuring production continuity. Tesla utilizes advanced software solutions for supply chain visibility, helping to track shipments in real time. However, obstacles such as port congestion, transportation disruption, and regulatory challenges can still arise. In addition, trade disputes and tariffs can affect material costs and availability. Tesla's adaptability in navigating these logistical hurdles plays a key role in sustaining operational integrity.
- Factors influencing logistical efficiency include:
- Transportation methods
- Regulatory environments
- Geographic challenges
Production Scalability and Flexibility
In today’s fast-evolving automotive landscape, production scalability and flexibility have become critical factors for success. Tesla exemplifies this through its unique approach, which aligns with the principles of innovative manufacturing. Scalability refers to the ability to increase production capacity in response to growing demand. Flexibility, meanwhile, relates to adjusting processes to accommodate product updates or shifts in consumer preferences. Together, these elements enable Tesla to maintain its competitive edge while ensuring operational efficiency.
Responding to Market Demand
The automotive market is influenced by various factors such as economic climate, consumer preferences, and technological advancements. Tesla has developed a robust system to respond swiftly to these changes. For instance, the company employs a modular production strategy which allows it to scale operations quickly based on demand forecasts and market trends.
By utilizing real-time data analytics, Tesla can monitor sales trends and adjust production schedules accordingly. This responsiveness minimizes excess inventory and mitigates risks associated with market fluctuations. Tesla’s factories can efficiently switch between different models—such as the Model 3 or Model Y—without major downtime, showcasing their flexible production lines. Often, companies face challenges during high demand periods, but Tesla seems to have strategies in place to manage these peaks effectively.
Adapting to Model Updates
The automotive industry is evolving, with electric vehicles leading the charge toward modernization. Adapting to model updates is essential for any manufacturer aiming to remain relevant. Tesla's production infrastructure is designed for rapid adaptations, allowing it to introduce updates without significant operational disruption.
When Tesla launches new features or updates, such as software upgrades or design enhancements, the company utilizes agile manufacturing techniques. This flexibility enables quick integration of new technologies into existing production lines. Moreover, feedback loops from customers and technicians inform Tesla about necessary adjustments, ensuring that updates meet user expectations.
The ability to adapt not only accelerates the product development cycle but also enhances customer satisfaction. By regularly updating models and incorporating new features, Tesla retains its position as a leader in the electric vehicle space.
"Tesla's capacity for rapid adaptation allows it to respond to consumer demands better than many competitors, creating a loyal customer base that values innovation."
In summary, production scalability and flexibility are not merely benefits for Tesla; they are vital to its long-term strategy. By strategically managing demand fluctuations and responding to market shifts, Tesla continues to shape the future of the automotive industry.
Quality Control Mechanisms
Quality control mechanisms are vital for maintaining the standard and performance that Tesla promises in all its vehicles. In the competitive automotive sector, ensuring product consistency is crucial. Effective quality control not only enhances customer satisfaction but also builds brand reputation and ensures compliance with safety regulations. Tesla’s commitment to quality encompasses multiple layers, from initial design through to the final inspection before delivery.
Inspection Procedures
Inspection procedures are a cornerstone of Tesla's approach to quality assurance. Every phase of production involves stringent checks to identify and rectify potential issues before they escalate. These procedures include:
- Material Verification: Before production begins, incoming materials undergo rigorous checks for quality, focusing on durability and performance.
- In-Process Inspections: During assembly, random inspections are conducted at various stages to ensure parts are assembled correctly and conform to specifications.
- Final Testing: Each vehicle is subjected to comprehensive testing to evaluate its performance under different conditions, simulating various driving scenarios.
By integrating these inspection processes, Tesla efficiently identifies faults early, reducing the likelihood of defects in delivered vehicles.
Emphasizing Safety and Reliability
Safety and reliability are paramount in automotive manufacturing, and Tesla places significant emphasis on these factors throughout its production cycle. The company establishes safety standards that exceed industry norms. Key aspects include:
- Robust Design Validation: Each model undergoes extensive simulations and crash tests to assess how it can protect occupants in case of an accident.
- Continuous Monitoring: Advanced data analytics are employed to monitor vehicle performance even after delivery. This data is crucial for improving future models and addressing any safety concerns swiftly.
- Feedback Loops: Customer feedback is actively solicited and analyzed. This allows Tesla to respond to any emerging issues, further enhancing reliability and trust.
"Trust and safety are crucial, so we must always uphold the highest standards."
Through these practices, Tesla not only enhances its product reliability but also reinforces consumer confidence, establishing a strong presence in the market. The interplay between rigorous inspection and commitment to safety constructs a solid foundation for Tesla's ongoing success.
Sustainability Initiatives in Production
Understanding sustainability initiatives in production is crucial, especially in the context of Tesla. As a frontrunner in electric vehicles, Tesla's approach to sustainable practices is not only about minimizing environmental damage but also about setting industry standards for the future.
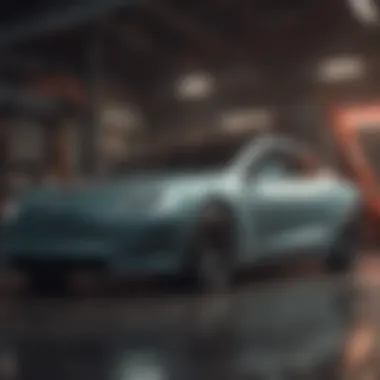
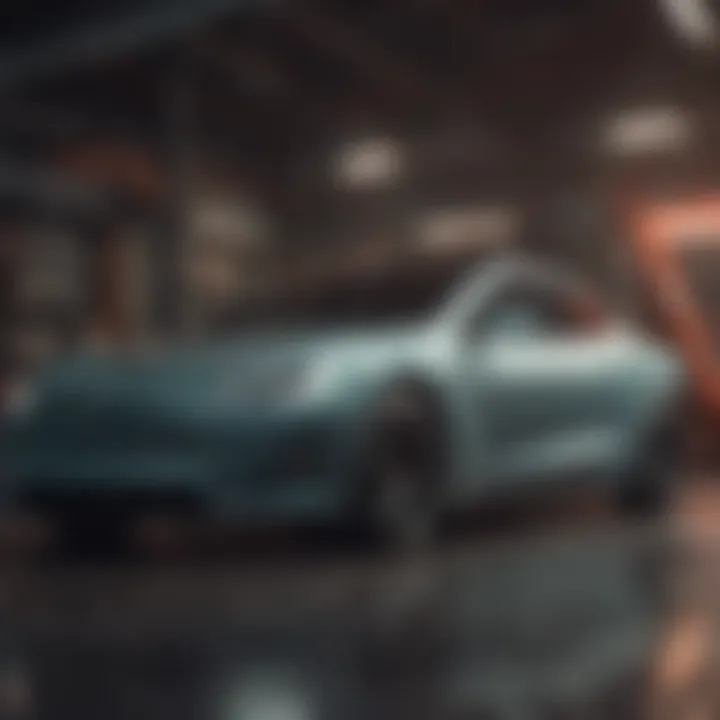
Environmental Impact Reduction
Tesla has taken significant steps to reduce its environmental footprint. This commitment is evident in various aspects of its production process. One key area of focus is the reduction of greenhouse gas emissions. Manufacturing electric cars inherently contributes to lower emissions during the vehicle lifecycle compared to traditional gasoline vehicles.
Besides that, Tesla has invested heavily in renewable energy sources for its production facilities. All Gigafactories operate on sustainable energy, a mix that often includes solar and wind power. By ensuring that the majority of their energy comes from these sources, Tesla reduces its reliance on fossil fuels. This strategy not only mitigates climate impact but also aligns with the company’s mission to accelerate the world’s transition to sustainable energy.
Another significant effort includes reducing water consumption in manufacturing. Water usage is often overlooked in production, yet Tesla has adopted practices that minimize wastage and promote efficient use. Such practices are essential as water scarcity becomes an increasing global concern.
"Sustainability is at the core of Tesla’s mission, shaping not just our products, but our entire operations."
Recycling and Reuse Strategies
Recycling and reuse represent another vital aspect of Tesla's sustainability program. The company aims to create a circular economy by reclaiming materials after a product's lifecycle. Tesla's battery recycling initiatives illustrate this commitment.
Lithium-ion batteries, used in most electric vehicles, contain valuable materials like lithium, cobalt, and nickel. Tesla has developed processes for recycling these batteries to extract and reuse these elements in new battery production. This reduces the need for mining, which is environmentally destructive and resource-intensive.
Tesla also focuses on reducing waste throughout its manufacturing plants. Implementing lean manufacturing techniques helps create less waste by optimizing the production flow. This involves many strategies, from improving production efficiency to ensuring that scraps are repurposed or recycled.
In addition, Tesla promotes longer-lasting products. The firm designs its vehicles to have an extended life cycle, minimizing the need for frequent replacements. This naturally leads to less waste and more sustainable consumer behavior, as buyers are encouraged to keep their vehicles longer.
Integrating these practices into production demonstrates Tesla's commitment to sustainability, reflecting an understanding that environmental stewardship is essential for long-term success. The company's progressive initiatives not only benefit the environment but also enhance its brand reputation, making it a leader in the automotive industry.
Future Production Projections
The examination of future production projections for Tesla provides crucial insight into the automotive industry's direction and Tesla's role within it. Understanding these projections can help industry stakeholders recognize the potential challenges and opportunities that lie ahead. As Tesla aims to maintain its leadership in the electric vehicle market, the relevance of its production forecasting cannot be understated. This analysis encompasses several key elements, including technology integration, market trends, and capacity planning.
Emerging Technologies and Trends
Emerging technologies are reshaping how Tesla approaches production. For instance, advancements in artificial intelligence and robotics are enhancing automation processes, reducing labor costs while increasing efficiency. The implementation of AI in manufacturing not only optimizes production lines but also improves quality control. Machine learning algorithms can analyze data from production processes in real-time, aiding decision-making and predictive maintenance.
In addition, developments in battery technology, such as solid-state batteries, are poised to significantly affect production dynamics. These new batteries could reduce charging time and extend the range of vehicles, which are critical factors in consumer adoption. Tesla is actively investing in research to leverage these technologies, thus positioning itself strategically for the inevitable evolution in electric vehicle specifications.
Furthermore, sustainable manufacturing practices are becoming paramount. Tesla is looking into renewable energy sources and recycling methods to minimize its environmental footprint. Emphasizing sustainability not only aligns with global trends but also enhances the brand value among environmentally conscious consumers.
Expected Production Growth
Production growth for Tesla is projected to escalate, driven by increasing demand for electric vehicles. As global governments push for greener transportation options and consumers become more aware of environmental issues, the market for electric vehicles is expanding rapidly. Tesla's goal to deliver more than a million cars annually by 2030 seems ambitious but attainable given its current market penetration and brand loyalty.
Factors contributing to this optimistic outlook include:
- Expansion of Gigafactories: Tesla continues to invest in Gigafactory developments around the world, which increases its production capabilities.
- New Model Launches: The introduction of models such as the Cybertruck and the Tesla Roadster can draw new customers into the fold, expanding market presence.
- Strategic Partnerships: Collaborations with other manufacturers and suppliers enable Tesla to secure resources and expand distribution.
"Tesla's growth strategy is fundamentally about execution, innovation, and staying two steps ahead of the competition."
Culmination
In this analysis, we have explored the intricate dynamics of Tesla's production strategies and methodologies. The conclusion encapsulates the essence of Tesla's manufacturing processes and their implications for the automotive industry. The key elements discussed include Tesla's innovative approaches, its robust supply chain management, and the sustainability measures that the company has embraced.
One of the significant benefits of understanding Tesla's production is recognizing how its methods set benchmarks for the entire industry. Tesla is not just a car manufacturer; it influences trends that others follow. Its continuous innovation ensures a quick adaptation to consumer demands, paving the way for advancements in electric vehicle technology.
Moreover, the emphasis on sustainability reflects a growing trend towards environmentally conscious production. This positions Tesla as a leader, appealing to a customer base that values green initiatives. As such, Tesla's operational model serves as a critical case study for aspiring companies looking to thrive in a competitive market
"Tesla’s approach to production embodies a blend of technology and sustainability, challenging traditional manufacturing norms."
Summary of Key Insights
The findings outlined in this article reveal several important insights about Tesla's production framework:
- Innovation: Tesla continually pushes boundaries, implementing cutting-edge technologies to improve efficiency.
- Gigafactories: The Gigafactory model significantly enhances production capabilities, allowing for increased efficiency and lower costs.
- Sustainability: The company prioritizes environmentally friendly practices within its production processes.
- Market Responsiveness: Tesla adapts promptly to shifts in market demand, showcasing its flexibility in production.
These insights underscore Tesla's unique position in the automotive sector, demonstrating how its production dynamics inform broader industry trends.
The Future of Tesla in Production
Looking ahead, Tesla's production landscape appears promising yet challenging. Emerging technologies, such as artificial intelligence and advanced robotics, are set to redefine production efficiencies. As we advance, it is crucial to note:
- Expansion of Gigafactories: New Gigafactories are expected to enhance production capabilities, meeting the growing global demand for electric vehicles.
- Innovative Materials: Development in material science will likely lead to lighter and more efficient vehicles, contributing to better energy consumption.
- Global Supply Challenges: Tesla must navigate supply chain complexities exacerbated by geopolitical factors.
Overall, the future of Tesla in production hinges on its ability to integrate these factors while staying true to its foundational principles of innovation and sustainability.